
After much thought, discussion, and research, I decided to go with rubber-based ink as the primary type of ink for my letterpress studio, mainly because it would take forever for me to finish a one-pound can and rubber-based ink is less likely to dry out in the can. I have stocked up on a bunch of Pantone bases and have armed myself with Pantone color guides to make custom mixes for client projects. I bought Van Son Rubber Base Plus in Rubine Red, Pantone Yellow, Process Blue, and Opaque White. I received a bunch of oil-based black as samples, so I will wait until I need more. (Of course, metallic colors only come in oil-based ink, so I got a can of metallic gold oil-based letterpress ink from Accent Ink as well.)
There was
a great discussion on Briarpress on inks, and one posting had a great technique at
measuring out the different colors for mixing. Jason used "dabs" to count out the different color parts. I used this technique in mixing the more complex custom mixes, although I do have to say that I did a fair amount of "eyeballing" as well.
I mixed the colors for three of my current projects, below. The first row is for a wedding invitation, the second is for a set of business cards for my client, and the third is for Joie Studio's business cards.
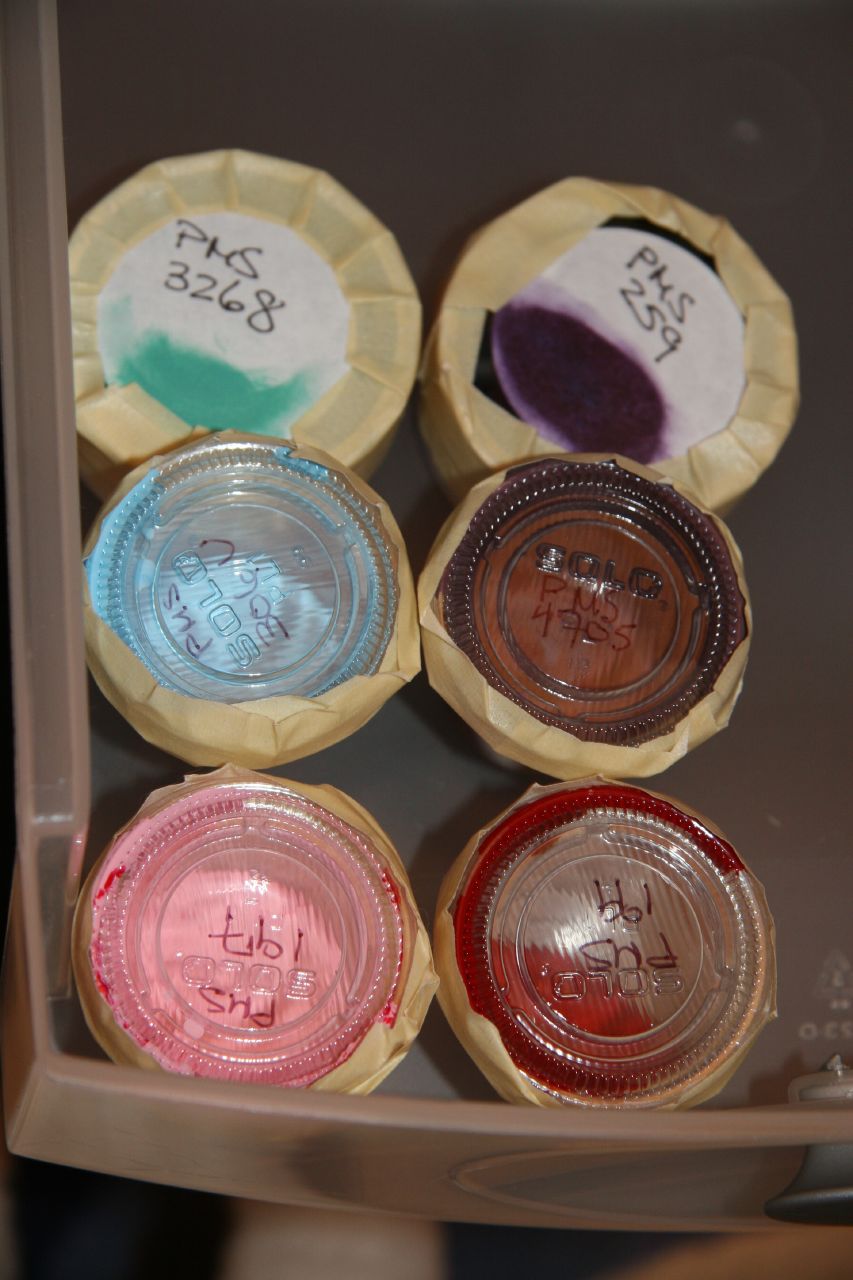
Finding containers to store the custom mixes has been an interesting scavenger hunt.
Dave Celani talks about using 4 oz cans and 5 oz tubes to store ink, but the amount I'm making is significantly smaller than 4 or 5 ounces. At letterpress class, we use old film canisters, but as I've completely switched to a digital photography setup here, that doesn't quite work out. I did find at a local restaurant supply store and a local craft store (Michael's!) some good storage options. For small amounts of ink that I want to save, I bought those little plastic containers and caps that to-go places put sauces in (about $5 for over 100 containers). These hold, according to the bag, 1.25 oz. I use a thin-tipped Sharpie to write the Pantone color number on the lid. I also bought wedding favor tins from my local craft store (Michael's, though I've seen them everywhere, including Target in the wedding section), which hold about twice as much as those little plastic containers. The wedding favor tins (about $20 for 30) have a clear top and also come with labels. I used the labels to smear some of the ink on and to write the Pantone number on. I tape these containers up so as to keep air out as much as possible.
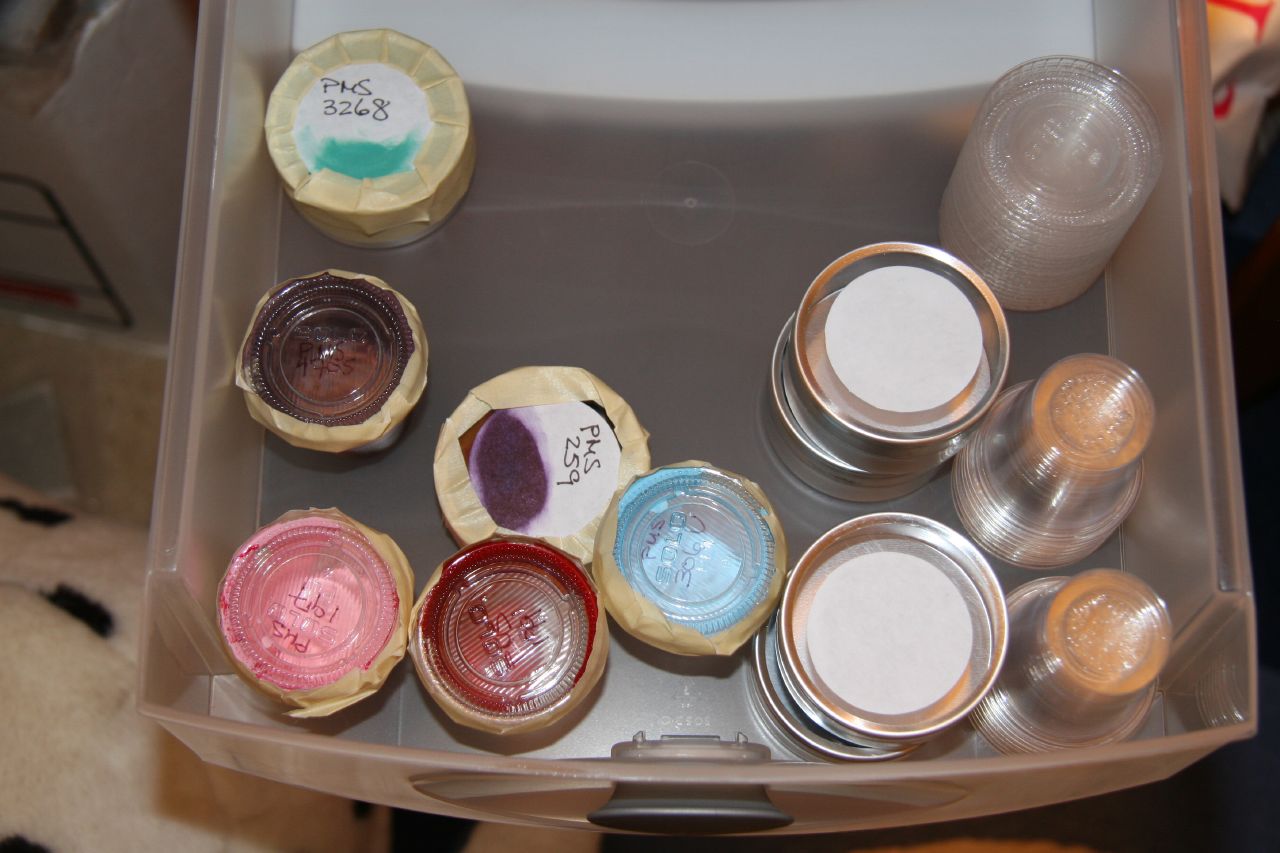
I am going to trade ink with a friend of mine who is also setting up a letterpress studio. We've bought some 4 oz cans and we luckily haven't had too much overlap yet on what colors we've bought because it would take either of us years to finish one of those cans of color!